5 DoF Robotic Arm
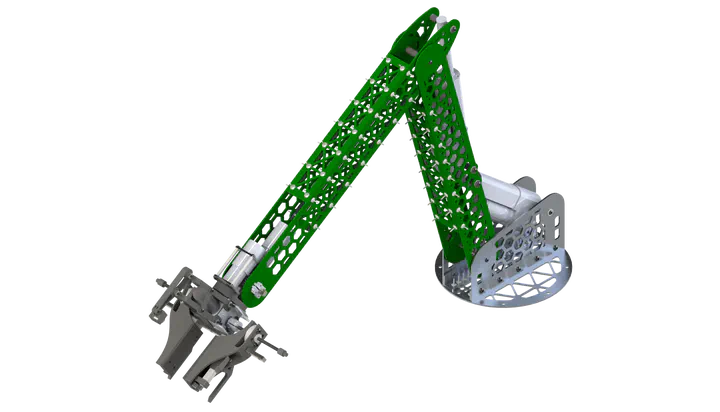
I built a 5 degree of freedom robotic arm for SC Robotics, my college mars rover team, competing in the University Rover Challenge. The design was based on a previous generation arm, but I revised the structure and designed a brand new end effector.
First, a video (0:45 for the arm):
Design
Previous Design
Structure
I decided to reconstruct the frame out of Garolite composite fiberglass to save weight. I also incorporated a box structure instead of the standoffs we used before, increasing rigidity.
End Effector and Wrist
The previous arm used a worm gear end effector, but because of the worn gears, it no longer pinched objects at the fingertips, similar to a worn out pair of pliers. To prevent this, I designed a new lead-screw-driven end effector.
Manufacturing
This project was my first exposure to such a saturated level of manufacturing. I manufactured almost all of the components on this arm using a CNC router, 3D printers, and other machines like bandsaws and drill presses. Here are a few images:
Here are some videos:
Competition
After our Systems Acceptance Review, we were admitted to the final competition in Utah. In this competition, there were two missions using the arm: the Extreme Retrieval Mission, a long-range task requiring retrieval of large objects, and the Equipment Servicing Mission, a short-range but very precise task.
Here is a picture from the Extreme Retrieval Mission (unfortunately, our drive train got stuck on a rock. But we had better luck next year!)
Here are some images from the Equipment Servicing Mission (13th place!):